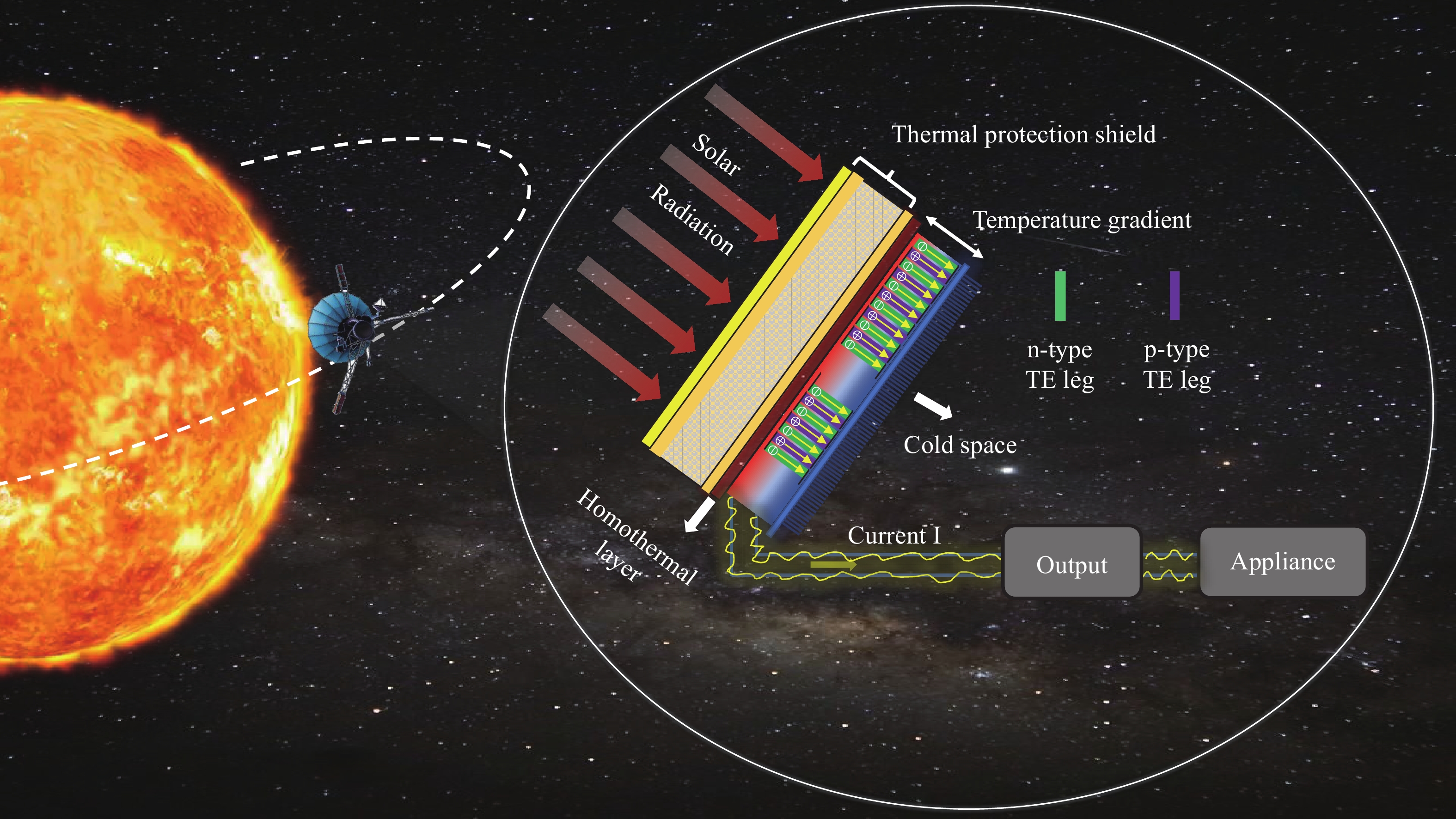
Citation: | Wang, Z. Y., Tian, J., Ge, Z. H., et al. 2025. A Dual Power Supply System for the Solar Close Observations and Proximity Experiments (SCOPE) Mission. Astronomical Techniques and Instruments, https://doi.org/10.61977/ati2025042. |
Previous solar probes have relied on solar energy for power, but in the near-solar environment, traditional solar panels are prone to overheating and radiation damage, increasing system complexity and reducing power reliability. This study introduces a dual power system integrating solar-thermal thermoelectric generation with photovoltaic technology. First, suitable thermoelectric materials are screened, the geometric structure of the thermoelectric devices is simulated, and then the fabricated thermoelectric devices are subjected to cyclic heating–cooling power generation tests and long-duration high-temperature power generation tests. The results demonstrate that a single thermoelectric device can stably provide 3.5 W of power with excellent cycling stability. Additionally, this study discusses design concepts for energy storage and intelligent energy management systems required by the dual-power system. Designed for the Solar Close Observations and Proximity Experiments mission, this dual-power supply system integrates the benefits of both to address demands under varying environmental conditions.
The Sun is the primary source of energy for Earth and the entire solar system. Studying the composition of the Sun, and its behavior and changes, is crucial for understanding its evolutionary history, periodic activities (such as sunspots and solar wind), and future variability. Solar activity, such as solar wind, solar flares, and coronal mass ejections, can have significant impacts on space weather, communication, navigation, and satellite systems[1]. Ultra-close proximity observations of the Sun can provide high-resolution data for studying the Sun and tracking the origins of hazardous space weather, offering a reliable foundation for theoretical studies on accurate space weather predictions. Furthermore, solar exploration missions not only drive advancements in space technology but also foster the development of ground-based technologies and material sciences, with potentially wide-reaching future applications.
In solar exploration missions, the power system of a spacecraft must overcome numerous significant challenges during its operation. First, after reaching the target orbit, the probe will encounter extreme high-temperature conditions. When approaching the Sun, the surface temperature of the probe may exceed
To overcome the challenges SCOPE will face, this paper proposes a hybrid power supply scheme that combines thermoelectric and solar power generation to maximize the utilization of the solar probe’s operating environment for stable and efficient power supply. In the power supply for the SCOPE mission[2-6], the spacecraft is protected by a core component, the heat shield, which directly faces the Sun to protect the spacecraft from damage caused by the high-energy radiation and high-temperature in the near-solar environment. In the shadowed area behind the heat shield, the shield itself can be used as a heat source for thermoelectric generation; using heat dissipation by radiation into space results in the required temperature gradient. This way, a temperature gradient of 400-500 °C can be formed across both ends of the thermoelectric generation module, which drives the conversion of heat into electrical energy.
Thermoelectric materials are functional materials characterized primarily by the Seebeck effect and the Peltier effect[7], using these two thermoelectric effects to efficiently convert heat energy into electrical energy and vice versa. Depending on the principle, thermoelectric materials are mainly applied in two broad categories[8]. Based on the Peltier effect, precise temperature control can be achieved by regulating input current, and is commonly applied to chip processors, biological temperature stabilization, and other areas requiring consistent cooling[9, 10]. Based on the Seebeck effect, heat can be converted into electrical energy in devices commonly referred to as thermoelectric generators (TEGs); this is an alternative energy generation technology with multiple application scenarios[11, 12]. Additionally, new flexible thermoelectric technology has outstanding potential for human-wearable devices[13, 14], human-computer interaction[15], and intelligent communication[16] thanks to its miniaturization, variability, and diversified design features.
A major application of TEGs is as a primary power source in extreme environments such as deep-space exploration, planetary surface missions, and deep-sea explorations. In 1954, the first thermoelectric generator (TEG), constructed using a Chromel-Constantan thermocouple, was employed to convert the heat from polonium-210 into electrical energy, marking the advent of the radioisotope thermoelectric generator (RTG)[17, 18]. By 1960, the National Aeronautics and Space Administration (NASA) began incorporating RTGs as energy sources for space exploration missions. Over the following decades, RTGs were used in numerous NASA missions, such as Galileo (1989, Jupiter), Ulysses (1990, solar mission), Cassini (1997, Saturn), New Horizons (2006, deep space), and Curiosity (2012, Mars)[19]. Each of these missions were powered by RTGs using Plutonium-238 as their heat source.
Since TEGs generate power without any moving parts, they provide vibration-free operation while avoiding damage to nearby systems over an extended operational lifespan. These unique advantages have fueled increasing interest in TEGs, particularly in the field of specialized environmental exploration engineering. The thermoelectric conversion efficiency (η) of TEGs is typically in the range of 10%, determined as
η=PcQh=Th−TcTh√1+Z¯T−1√1+Z¯T+TcTh |
where T̅ is the average temperature, Th and Tc are the temperatures at the hot and cold sides, respectively, and ZT is the dimensionless thermoelectric figure of merit for the thermoelectric material. There are three main approaches to improve the thermoelectric conversion efficiency of TEGs: thermoelectric materials can be developed with a ZT value greater than 1; the structure of the TEG module can be optimized; and a large temperature difference can be ensured across the TEG module for the highest possible thermoelectric efficiency[20].
The ZT value is determined by the intrinsic properties of the thermoelectric material, as shown by
ZT=S2σκele+κlatT, |
where S is the Seebeck coefficient, σ is the electrical conductivity, κele is the carrier thermal conductivity, and κlat is the lattice thermal conductivity of the thermoelectric material. To achieve the highest ZT value possible, a variety of new materials with excellent thermoelectric potential have been discovered, such as Bi2Te3-based and Mg3Bi2-based thermoelectric materials with excellent thermoelectric performance at room temperature, PbQ (Q = S, Se, Te)-based, SnQ (Q = S, Se, Te)-based, GeTe materials for mid-temperature applications, and skutterudites, which are Half-Heusler materials with remarkable ZT values at high temperatures. In addition, numerous optimization strategies have been designed for various thermoelectric material systems. For example, band engineering[21] is used to adjust the band structure of materials, increase the density of states, optimize the carrier concentration, and enhance the Seebeck coefficient. Other potential methods include nanostructure engineering[22], phase engineering, defect engineering[23], high-entropy engineering[24], and the phonon-liquid-electron-crystal (PLEC) strategy[25], which introduces multi-scale phonon scattering centers to optimize the thermal transport properties of materials. Among these, single crystal SnSe-based thermoelectric materials, since their first report, have exhibited a ZT value as high as 2.6, sparking significant research interest. However, due to the inherent dissociation characteristics of SnSe crystals, their mechanical properties are weak, making processing a significant challenge and limiting their large-scale application. It is noteworthy that polycrystalline SnSe materials, after doping modifications, can also achieve ZT values greater than 2, and have significantly improved mechanical properties compared to single-crystal SnSe materials, fulfilling the needs for production and processing.
Furthermore, the structural design of thermoelectric generation modules is also a crucial factor that cannot be ignored, and needs to be carried out according to the design logic shown in Fig. 2[26]. The traditional design model for thermoelectric generation modules follows a π-shaped structure, where n-type and p-type thermoelectric legs are alternately connected end-to-end via weldable electrodes, forming a series circuit. Due to its simple modular design, ease of assembly and use, as well as lower production costs, this type of structure is widely used for thermoelectric generation modules. Meanwhile, the requirements of long service life, high module stability, and high-power generation efficiency for space exploration missions have driven the development of segmented device designs based on the π-shaped structure. This innovative design concept can achieve performance beyond that of traditional thermoelectric generation modules by selecting and matching thermoelectric materials. Additionally, segmented thermoelectric generation modules achieve thermal-physical property matching by selecting p-type and n-type materials with similar coefficients of thermal expansion, reducing the risk of stress damage to the device caused by thermal stress mismatch. However, in comparison with traditional thermoelectric power generation modules, the production and assembly process of segmented modules is more complex, which increases production costs and requires comprehensive stability assessments before operation, which increases time costs.
In the structural optimization of thermoelectric modules, the geometric dimensions of thermoelectric legs are a critical component. Given the differences in the electrical and thermal transport properties of the p-type and n-type thermoelectric materials in the module, we select polycrystalline SnSe as the thermoelectric leg material for the SCOPE power supply scheme, constructing a π-shaped thermoelectric device model with two pairs of thermoelectric legs for geometric optimization simulations, to achieve the best device performance, as shown in Fig. 3. Using the finite element simulation method, via the COMSOL software package, we model a temperature gradient with a hot-end temperature of 673 K and a cold-end temperature of 273 K, to optimize the aspect ratio (A/H) of the thermoelectric leg height to its cross-sectional area.
As shown in Figs. 3a and 3b, increasing the load resistance leads to a rise and subsequent fall in the maximum output power (Pmax) and thermoelectric conversion efficiency (η) across devices of all sizes, peaking at a specific dimension. However, when the load resistance is fixed, Pmax decreases as the A/H ratio drops, whereas η increases, demonstrating that Pmax and η cannot be maximized concurrently for a single device dimension. we perform additional simulations under constant load resistance, to examine the internal resistance of devices with differing dimensions. As shown in Figs. 3c and 3d, as the A/H ratio increases, the internal resistance (Rin) of the device gradually decreases, while higher Rin correlates with a drop in Pmax. Meanwhile, ηmax remains steady at 12%. Thus, Pmax and ηmax can be achieved by increasing A/H under a constant hot-cold temperature difference. Nonetheless, an excessively high A/H ratio limits the thermoelectric leg height in micro-scale thermoelectric modules, while overly short legs hinder the establishment of a sufficient temperature gradient between the hot and cold ends. Therefore, considering manufacturability, we select an A/H ratio of 3.6 for assembling the thermoelectric device.
Based on the simulation results, we designed and created thermoelectric devices, and conducted power generation tests on individual thermoelectric devices, with the results presented in Fig. 4. The first test is the cyclic heating power generation test. A specially designed temperature-controlled heating plate is used as the heat source for assessment, and a water-cooling system is used at the cold end, to maintain the temperature difference between the two ends of the thermoelectric device. The hot end temperature was set at 643 K and maintained for 6 hours. Then it was cooled down to 300 K and 20 cycles were conducted. The test results are shown in Fig. 4a. During 20 cycles of heating, the thermoelectric module can stably provide a power supply of 3.5 W. In addition, the thermoelectric module was tested for long-term heat preservation and power generation using the same assessment device, i.e., the hot end was heated to 643 K and maintained for 18 hours. The test results are shown in Fig. 4b. During the heat preservation process, the thermoelectric module can also stably provide 3.5W of electricity. Subsequently, we characterized the phase structure of the thermoelectric materials in the thermoelectric module after x cycles (x = 0, 1, 3, 5, 10, 15, 20) of tests, to determine their stability, with results shown in Figs. 4c and 4d. The X-ray diffraction peaks of all the tested SnSe thermoelectric materials were in good agreement with the standard card. No diffraction peaks of the impurity phase or obvious lattice distortion were observed, indicating that the phase structure of the samples was stable after cyclic heating and cooling.
By placing the thermoelectric generation module on the back of the thermal protection shield of the solar probe, high-energy radiation and particle impacts can be effectively shielded. However, this increases the requirements for thermal conduction efficiency between the hot end of the thermoelectric power module and the heat shield. To achieve uniform distribution of heat flow and avoid local hotspots that cause uneven heating of the thermoelectric generation module, a heat spreading material should be applied to the external surface of the hot side of the thermoelectric generation module, allowing heat to diffuse evenly across the contact area of the entire module. Meanwhile, the hot side surface should also maximize heat absorption from the heat shield and transfer it to the thermoelectric material. This can be achieved by coating the hot side surface with a high-thermal-conductivity coating, to optimize the thermal contact resistance at the interface.
On the basis of the above two requirements, we select a carbon-based coating (e.g., graphene-based materials) as the contact layer between the thermoelectric generation module and the thermal protection shield. Carbon-based materials have been widely used in the field of heat dissipation in electrical equipment and industrial equipment, due to their excellent thermal conductivity (taking graphene as an example, thermal conductivity is in the range of
In a similar “touch the Sun” mission, the NASA PSP is preparing to plunge to within 4 million miles of the solar surface and will be subjected to levels of heat and radiation unprecedented for spacecraft to endure, offering previously unavailable observations and allowing close study of the Sun. The energy source of the PSP is provided by a well-designed, actively cooled solar panel. This solar panel consists of two components: Two solar panels placed on either side of the PSP, covering a total area of 1.55 m², and a radiation heat sink situated behind the thermal protection module.
Photovoltaic cells, commonly considered the most efficient solar energy conversion technology, are available in different forms for power generation. They can operate as standalone units or be interconnected in series to create extensive solar cell arrays. The primary mechanism of power generation in solar cells involves semiconductor p-n junctions. When sunlight strikes the p-n junction, it creates hole-electron pairs, prompting electrons to migrate from the p-region to the n-region, thereby producing an electrical current in the circuit when combined with an external load. This current originates from the absorption of high-energy photons by the photovoltaic material, while lower-energy photons, unable to be absorbed, are instead converted into heat. Additionally, as a result of the inherent resistance of silicon, the current flow causes heating within the solar cells.
During operation, the heat generated by the solar panels and solar radiation is carried by one gallon of circulating water, to the radiators for cooling. When closest to the Sun, the spacecraft receives solar intensity roughly 475 times stronger than that in Earth orbit. Therefore, the surface temperature of the solar cells in operation can become very high, significantly reducing power conversion efficiency and severely shortening the lifespan of the cells.
It is essential to find new technologies to address the thermal management challenges of photovoltaic power systems. Liu et al. proposed an advanced thermal management system (ATMS), with adaptive control based on the characteristics of the SCOPE mission[30]. A benefit of an advanced fluid cooling system and modular design is that changes in the thermal environment, where the detector, solar array, and payload are located, can be responded to quickly.
For missions such as close solar probes, that make full use of received thermal energy, we have designed a dual-power supply system where thermoelectric generation serves as the primary power source, with solar power generation as a secondary source. Although thermoelectric generation can harness the temperature gradient generated by the thermal protection shield for power generation, its efficiency is limited by the temperature difference and thermal conductivity, and the output power may not be sufficient to meet peak load demands. Solar power generation, being a well-established energy conversion technology, can provide an additional energy source for the power system. The deep space environment is complex and variable. When the spacecraft operates at a greater distance from the Sun, the temperature on the rear of the thermal protection shield decreases, causing a reduction in the efficiency of the thermoelectric generator. In these situations, solar power generation can assume part of the power supply responsibility, ensuring the proper functioning of essential systems. Moreover, when sunlight conditions are favorable and thermal management stress is low, incorporating solar power generation can decrease the prolonged high-load operation of the thermoelectric generator, prolonging its lifespan, and providing additional energy reserves for long-duration missions. Therefore, a dual power supply system is an effective solution. When solar radiation is less than 300 times that near the Earth, solar panels are used to supply power. When the intensity of solar radiation exceeds 300 times that near the Earth, solar panels will retract and fold, and all required energy will be provided by thermoelectric modules.
To accommodate fluctuations in the thermoelectric and solar power generation, an energy storage and intelligent energy management system are also critical components of this power supply scheme, as shown in Fig. 5. The system needs to have efficient energy distribution capabilities and dynamic adaptability to balance the differences between the two power generation methods and optimize the energy use efficiency[31].
In the energy collection and conversion module, an independent thermoelectric power generation input interface and a solar cell input interface are selected and connected to DC-DC converters. A multi-channel DC-DC converter is then used to adjust the output voltage of the two power generation methods to the working voltage of the energy storage system (e.g., 3.7 V or 7.4 V) for voltage regulation and integration. An intelligent switching network is used to determine the power supply method for the energy storage system, based on preset conditions, giving priority as required. For the energy storage devices, after comparing various typical battery types used in space missions, such as lithium-ion batteries (LIBs), lithium-polymer batteries, nickel-metal hydride (NiMH) batteries, nickel-cadmium (NiCd) batteries, and solid-state batteries, we select the high-temperature LIBs for this power supply scheme, for their current higher technological maturity. Compared with traditional nickel-chromium batteries, LIBs have higher energy density, a longer cycle life, and shorter charging time, which can provide more stable power support for the detector. At the same time, the lower quality makes it suitable for weight-sensitive detectors. In the SCOPE mission, the LIBs not only face high temperatures generated by the exothermic reaction during the charging and discharging process, but also faces the challenge of increased operating temperature near the sun. Fortunately, the question of how to improve the high temperature stability of LIBs has attracted attention in the research community in recent years. Yu et al. improved the electrochemical performance of the cathode by adding 3-triethoxysilylpropylsuccinic acid anhydride to the electrolyte to remove water and hydrogen fluoride, and after holding at 358 K for 8 hours, the thickness expansion rate was reduced from 60% to 23%, which improved the long-term stability of LIBs[32]. Li et al. inhibited high-temperature side reactions by introducing anionic acceptor additives, allowing high-temperature LIBs to have long-term stability and high-temperature tolerance. After 100 cycles at 328 K, the capacity retention rate reached 84%[33]. In addition, the study of new high-temperature-resistant electrolytes provides a pathway for moving from room temperature lithium-ion technology to extreme temperature applications. Leela et al. reported a battery chemical system based on non-flammable phosphonium ionic liquid, which provides a stable electrode-electrolyte interface, achieving electrochemical performance up to 398 K safely at high temperatures. The battery sample maintained a Coulombic efficiency of 99.5% after 300 cycles at 373 K[34]. Zhang et al. achieved a Coulombic efficiency of 98.8% for lithium-copper batteries using solvent-free molten salt electrolytes after 500 cycles at 353 K[35].
The constituent elements of lithium-ion batteries are low in mass, meaning that they are highly vulnerable to damage from high-energy radiation. Consequently, special shielding designs to protect the batteries from solar energetic particles are necessary to preserve their operational lifespan. To ensure mission safety, multiple battery sets are installed to provide redundancy and avoid any power interruptions caused by single-point failures. During mission execution, the dynamic energy management module adjusts the priority of power generation methods, performing real-time monitoring and prediction for energy scheduling. By considering factors such as distance, temperature differences, power generation efficiency, and load requirements, the power generation ratio and supply sequence are dynamically adjusted. When farther from the Sun, thermoelectric generation efficiency decreases, and solar power generation is primarily used to supply the energy storage system; when closer to the Sun, thermoelectric generation power increases, and the attitude of solar panels is adjusted to reduce thermal management pressure, prioritizing thermoelectric generation. During low-load conditions, excess energy is stored, and under high-load conditions, direct power supply is prioritized to reduce the output pressure on the energy storage system.
Our proposed power supply scheme combines thermoelectric generation and solar power, effectively addressing the challenges of energy fluctuations and environmental changes in the SCOPE mission, through intelligent energy management and efficient energy storage systems. Thermoelectric generation uses the temperature difference between the heat shield and the deep space environment to provide stable power for the spacecraft, while solar power serves as an additional energy source under suitable conditions, optimizing energy use efficiency. The design of multiple battery redundancy mechanisms and intelligent scheduling ensures the efficiency and stability of the power supply system under various operating conditions. Additionally, considering the impact of high-energy radiation on battery life, our scheme incorporates high-temperature lithium-ion batteries and specialized shielding to ensure mission safety and long-term battery stability. Overall, this scheme enhances system reliability and continuous energy supply, providing a promising method for energy management in the SCOPE mission.
初始空段落
This work is supported by National Key R&D Program of China (No.2022YFF0503804).
Zi-Yuan Wang and Zhen-Hua Ge conceived the research concept and designed the experimental framework. Zi-Yuan Wang performed experiments and analyzed the data. Zhen-Hua Ge and Jing Feng established simulation and evaluation platforms for the thermoelectric generation modules. Zi-Yuan Wang and Jiang Tian conducted performance testing of the generation modules. Zi-Yuan Wang drafted the manuscript. Zhen-Hua Ge critically reviewed and revised the manuscript. All authors read and approved the final version of the manuscript.
The authors declare no competing interests.
[1] |
Lin J. , Soon W. , Baliunas S. L. 2023. Theories of solar eruptions: a review. New Astronomy Reviews, 47(2): 53−84
|
[2] |
Lin J., Feng J., Ge Z., et al. 2025. The Solar Close Observations and Proximity Experiments (SCOPE) mission. Astronomical Techniques and Instruments, 2(3): 1−27.
|
[3] |
Lin J., Huang S., Li Y., et al. 2021. In Situ Detection of the Solar Eruption: Lay a Finger on the Sunormalsize. Chinese Journal of Space Science, 41(2): 183−210.
|
[4] |
Lin J. , Huang S. -j. , Li Y. , et al. 2021. In Situ Detection of the Solar Eruption: Lay a Finger on the Sun. Chinese Astronomy and Astrophysics, 45(3): 301-351.
|
[5] |
Lin J., Lu X., Chen Y., et al. 2024. Solar Close Observations and Proximity Experiments. Aerospace Shanghai (Chinese and English), 41(5): 1−10.
|
[6] |
Lin J. , Wang M. , Tian H., et al. 2019. In situ Measurements of the Solar Eruption. SCIENTIA SINICA Physica, Mechanica & Astronomica, 49(5): 059607
|
[7] |
Bell L. E. 2008. Cooling, Heating, Generating Power, and Recovering Waste Heat with Thermoelectric Systems. Science, 321(5895): 1457−1461. doi: 10.1126/science.1158899
|
[8] |
DiSalvo F. J. 1999. Thermoelectric Cooling and Power Generation. Science, 1999, 285(5428): 703-706.
|
[9] |
Liu D., Wang D., Hong T., et al. 2023. Lattice plainification advances highly effective SnSe crystalline thermoelectrics. Science, 380(6647): 841−846. doi: 10.1126/science.adg7196
|
[10] |
Qin Y., Qin B., Hong T., et al. 2024. Grid-plainification enables medium-temperature PbSe thermoelectrics to cool better than Bi2Te3. Science, 383(6688): 1204−1209. doi: 10.1126/science.adk9589
|
[11] |
Jiang B., Yu Y., Cui J., et al. 2021. High-entropy-stabilized chalcogenides with high thermoelectric performance. Science, 371(6531): 830−834. doi: 10.1126/science.abe1292
|
[12] |
Shi X., Song S., Gao G., et al. 2024. Global band convergence design for high-performance thermoelectric power generation in Zintls. Science, 384(6697): 757−762. doi: 10.1126/science.adn7265
|
[13] |
Du Z., Li L., Shen G. 2025. An Ultra-Thin Wearable Thermoelectric Paster Based on Structured Organic Ion Gel Electrolyte. Nano-Micro Letters, 17(1): 204. doi: 10.1007/s40820-025-01721-4
|
[14] |
Miao L., Zhu S., Liu C., et al. 2024. Comfortable wearable thermoelectric generator with high output power. Nature Communications, 15(1): 8516. doi: 10.1038/s41467-024-52841-1
|
[15] |
Kim C. S., Yang H. M., Lee J., et al. 2018. Self-Powered Wearable Electrocardiography Using a Wearable Thermoelectric Power Generator. Acs Energy Letters, 3(3): 501−507. doi: 10.1021/acsenergylett.7b01237
|
[16] |
Li Y., Wang W., Cui X., et al. 2025. Self-Powered Machine-Learning-Assisted Material Identification Enabled by a Thermogalvanic Dual-Network Hydrogel with a High Thermopower. Small, 21(1): 2405911. doi: 10.1002/smll.202405911
|
[17] |
Robert L. C. , Gary L. B. 2011. U. S. Space Radioisotope Power Systems and Applications: Past, Present and Future. In Radioisotopes, Nirmal, S. , Ed. IntechOpen: Rijeka; p Ch. 22.
|
[18] |
Terranova M. L. 2022. Nuclear Batteries: Current Context and Near-Term Expectations. International Journal of Energy Research, 46(14): 19368−19393. doi: 10.1002/er.8539
|
[19] |
Zoui M. A., Bentouba S., Stocholm J. G., et al. 2020. A Review on Thermoelectric Generators: Progress and Applications. Energies, 13(14): 3606. doi: 10.3390/en13143606
|
[20] |
Shi X. -L. , Zou J. , Chen Z. -G. 2020. Advanced Thermoelectric Design: From Materials and Structures to Devices. Chemical Reviews, 120(15): 7399−7515
|
[21] |
Deng Q. , Wen J. , An X. , et al. 2025. Thermoelectric cooling and low-temperature power generation in n-type PbTe enabled by band flattening and entropy engineering. Chemical Engineering Journal, 506(160319.
|
[22] |
Kanatzidis M. G. 2010. Nanostructured Thermoelectrics: the New Paradigm. Chemistry of Materials, 22(3): 648−659. doi: 10.1021/cm902195j
|
[23] |
Zhao C., Li Z., Fan T., et al. 2020. Defects Engineering with Multiple Dimensions in Thermoelectric Materials. Research, 2020: 9652749.
|
[24] |
Moshwan R. , Shi X. -L. , Liu W. -D. , et al. 2024. Entropy Engineering: An Innovative Strategy for Designing High-Performance Thermoelectric Materials and Devices. Nano Today, 58: 102475.
|
[25] |
Zhang Z. , Zhao K. , Wei T. -R. , et al. 2020. Cu2Se-Based Liquid-Like Thermoelectric Materials: Looking Back and Stepping Forward. Energy & Environmental Science, 13(10): 3307−3329
|
[26] |
Zhang Q., Liao J., Tang Y., et al. 2017. Realizing a Thermoelectric Conversion Efficiency of 12% in Bismuth Telluride/Skutterudite Segmented Modules through Full-Parameter Optimization and Energy-Loss Minimized Integration. Energy & Environmental Science, 10(4): 956−963.
|
[27] |
Balandin A. A. 2011. Thermal properties of graphene and nanostructured carbon materials. Nature Materials, 10(8): 569−581. doi: 10.1038/nmat3064
|
[28] |
Yu G. -C. , Wu L. -Z. , Feng L. -J. 2015. Enhancing the thermal conductivity of carbon fiber reinforced polymer composite laminates by coating highly oriented graphite films. Materials & Design, 88: 1063−1070
|
[29] |
Kumar S. , Tripathi A. , Khan S. A. , et al. 2014. Radiation stability of graphene under extreme conditions. Applied Physics Letters, 105(13).
|
[30] |
Liu L., Bao K., Feng J., et al. 2024. Design and analysis of an advanced thermal management system for the solar close observations and proximity experiments spacecraft. Astronomical Techniques and Instruments, 1(1): 52−61. doi: 10.61977/ati2024007
|
[31] |
Shen Z. -H. , Ni H. , Ding C. , et al. 2021. Improving the Energy-Conversion Efficiency of a PV–TE System With an Intelligent Power-Track Switching Technique and Efficient Thermal-Management Scheme. IEEE Transactions on Components, Packaging and Manufacturing Technology, 11(6): 963−973
|
[32] |
Zhang C. -M. , Ge C. -Y. , Zhu X. -Q. , et al. 2025. A novel electrolyte additive for improving the stability of layered oxide cathode material-based lithium-ion batteries under high temperature and voltage conditions. New Journal of Chemistry, 49(21): 9023−9034
|
[33] |
Yang K., Zhao D., Wang H., et al. 2025. Promoting long-term stability and high-temperature tolerance of lithium-ion batteries by introducing anion receptor additives into electrolyte. Journal of Energy Storage, 117: 116094. doi: 10.1016/j.est.2025.116094
|
[34] |
Nagarajan S., Hwang S., Jaye C., et al. 2025. Investigation of electrode-electrolyte interfaces to enable non-flammable Li-ion batteries operating up to 125°C with liquid electrolyte. Cell Reports Physical Science, 6(5): 102597. doi: 10.1016/j.xcrp.2025.102597
|
[35] |
Yan S., Yao N., Liu H., et al. 2025. Molten salt electrolytes with enhanced Li+-transport kinetics for fast-cycling of high-temperature lithium metal batteries. Energy & Environmental Science, 18(4): 1696−1706.
|